|
|
نوشته شده توسط : رسول دلاکان
متن کامل فلز برنج را می توانید با کلیک بر روی عبارت ((فلز برنج)) مشاهده نمایید.
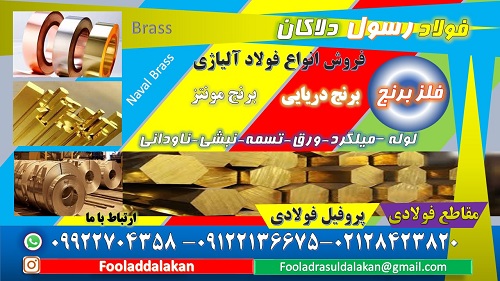
فلز برنج – برنج (Brass) ترکیبی آلیاژی از مس و روی است. معمولاً ترکیب این آلیاژ با عناصر دیگر را برنز می گویند. گاهی اوقات نام عنصر آلیاژی به همراه برنز آورده می شود. برای مثال: برنز قلع دار یا برنز فسفردار. صدها نوع ترکیب گوناگون در هر یک از این گروه ها وجود دارد.
با تغییر مقدار روی، خواص آلیاژهای مس – روی نیز تغییر می کند. برنج های مس – روی که عناصر اضافی مانند قلع، آلومینیوم، سیلیسیم، منگنز، نیکل و سرب دارند به عنوان برنج های آلیاژی نام دارند.
برنج از مدت ها پیش حتی قبل از تاریخ مورد شناخت بود. در آن زمان که انسان هنوز فلز روی را نمی شناخت. با ذوب کردن مس همراه با کالامین (سنگ معدن فلز روی) برنج تولید می کرد.
برنج معمولاً قابلیت چکش خواری بیشتری نسبت به مس و روی دارد و دمای ذوب آن تقریباً بین 900 تا 940 درجه سانتی گراد است. البته سختی و نرم بودن آن می تواند با تغییر نسبت مخلوط مس و روی تغییر کند. مس داخل برنج (از طریق اولیگو دینامیک) خاصیت میکروبکشی به آن می دهد. به همین خاطر از برنج به عنوان دستگیره و دیگر فلزات رایج در بیمارستان استفاده می کنند.
امروز تقریباً 90% از فلزات برنج بازیافت می شوند. چون فلز برنج خاصیت مغناطیسی کمی دارد و به راحتی می توان آن را از فلزاتی که معمولاً با آنها مخلوط می شود جدا کرد. بدین ترتیب برنجی که می گردد را دوباره بازیافت می کنند. چگالی برنج ریختگی در حدود 8400 تا 8700 کیلوگرم بر مترمکعب می باشد.
فولاد رسول دلاکان
با سالها تجربۀ ارزشمند و گرانبها در عرصه تأمین و توزیع انواع ورق آلیاژی و انواع فولاد آلیاژی. با گواهینامه ها و آنالیزهای معتبری با ضمیمه نمودن آن محصولاتش به مشتریان خویش ارائه داده است. توانسته، رضایتمندی مشتریان خویش را همواره فراهم آورد.
صنعتگر شریف و گرامی از اینکه ما را جهت خرید کالا (فولاد آلیاژی) مورد نیاز خویش. انتخاب می نمایید از شما سپاسگزاریم.
ارتباط با ما
02128423820 -09122136675 – 09922704358
واتس آپ: 09122136675
اینستاگرام: fooladdalakan
فکس : 02128423820
ایمیل : fooladrasuldalakan@gmail.com
:: برچسبها:
فلز برنج ,
برنج ,
آلیاژ برنج ,
Brass ,
مقاطع فولادی ,
پروفیل فولادی ,
تسمه فولادی ,
میلگرد فولادی ,
لوله فولادی ,
ورق فولادی ,
فولاد آلیاژی ,
فولاد زنگ نزن ,
فولاد ضد زنگ ,
فولاد ضد خوردگی ,
,
:: بازدید از این مطلب : 947
|
امتیاز مطلب : 10
|
تعداد امتیازدهندگان : 5
|
مجموع امتیاز : 5
تاریخ انتشار : دو شنبه 19 مهر 1400 |
نظرات ()
|
|
نوشته شده توسط : رسول دلاکان
متن کامل فولاد بلبرینگ را می توانید با کلیک بر روی عبارت ((فولاد یاتاقان)) مشاهده نمایید.
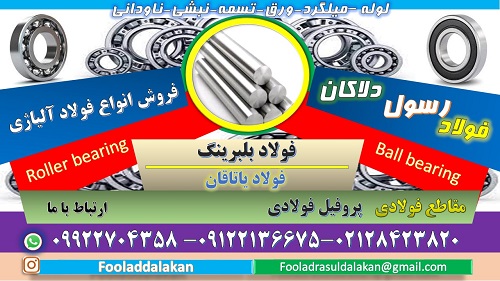
سپس با عملیات حرارتی، ساختار فازی و سختی مناسبی در آنها ایجاد می کنند. این قطعات به صورت سنگ زنی و پولیش شده مورد استفاده قرار می گیرند.
فولادهای بلبرینگ و رولبرینگ باید و دارای مقاومت مکانیکی بالا، پایداری در مقابل فرسایش و حد خستگی خیلی بالایی باشند. زیرا اجزاء یک بلبرینگ و رولبرینگ در موقع کار، بارهای متناوب بزرگی را تحمل می نماید. فولادهای بلبرینگ باید تا حد امکان خالص و عاری از آخال های غیر فلزی. حفره ها و هر نوع نقص دیگر که می تواند محل تمرکز تنش بوده و موجب شکست قطعه شود، باشد.
فولاد بلبرینگ
برای ساخت بلبرینگ و رولبرینگ از 5 گروه فولادی استفاده می شود:
- فولادهای بلبرینگ و رولبرینگ سخت کاری اند. از نوع فولادهای پرکربن کروم دار
- فولادهای بُلبرینگ و رولبرینگ سخت کاری سطحی است از نوع فولاد کم کربن کم آلیاژ یا آلیاژ متوسط با قابلیت کربن دهی سطحی
- فُولادهای بلبرینگ و رولبرینگ سخت کاری القایی از نوع فولادهای کربن متوسط کم آلیاژ با قابلیت سخت کاری القایی
- فولادهای بلبرینگ و رولبرینگ زنگ نزن کروم دار
- فولادهای بلبرینگ و رولبرینگ با سخت کاری دما بالا از نوع فولادی آلیاژی
هرکدام از این گروه ها، شامل گریدهای مختلفی از فولادهای قابل عملیات حرارتی سخت کاری. با ویژگی های مناسب برای استفاده در ساخت اجزای بلبرینگ و رولبرینگ هستند.
فولاد رسول دلاکان
با سالها تجربۀ ارزشمند و گرانبها در عرصه تأمین و توزیع انواع ورق آلیاژی و انواع فولاد آلیاژی. با گواهینامه ها و آنالیزهای معتبری با ضمیمه نمودن آن محصولاتش به مشتریان خویش ارائه داده است. توانسته، رضایتمندی مشتریان خویش را همواره فراهم آورد.
صنعتگر شریف و گرامی از اینکه ما را جهت خرید کالا (فولاد آلیاژی) مورد نیاز خویش. انتخاب می نمایید از شما سپاسگزاریم.
ارتباط با ما
02128423820 -09122136675 – 09922704358
واتس آپ: 09122136675
اینستاگرام: fooladdalakan
فکس : 02128423820
ایمیل : fooladrasuldalakan@gmail.com
:: برچسبها:
فولاد بلبرینگ ,
فولاد رولبرینگ ,
فولاد کربنی ,
مقاطع فولادی ,
ball bearing ,
فولاد ضد زنگ ,
فولاد های کروم دار ,
پروفیل فولادی ,
میلگرد فولادی ,
لوله فولادی ,
تسمه فولادی ,
ورق فولادی ,
فولاد زنگ نزن ,
فولاد سختکاری ,
فولاد آلیاژی ,
فولاد کم آلیاژ ,
فولاد پر کربن ,
,
:: بازدید از این مطلب : 920
|
امتیاز مطلب : 19
|
تعداد امتیازدهندگان : 5
|
مجموع امتیاز : 5
تاریخ انتشار : دو شنبه 19 مهر 1400 |
نظرات ()
|
|
نوشته شده توسط : رسول دلاکان
متن کامل قلع را می توانید با کلیک بر روی عبارت ((فلز قلع)) مشاهده نمایید.
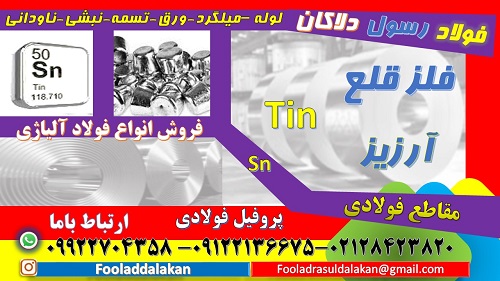
قلع یا آرزیز (Tin) عنصری است شیمیایی با علامت اختصاری sn. و با شماره 50 در جدول اتمی، هم گروه با نافلزاتی چون، کربن، سیلیسیم و ژرمانیوم است. بنابراین انتظار می رود که به لحاظ خواص شیمیایی، تا حدودی با این عناصر شباهت داشته باشد.
این فلز نقره ای رنگ خاصیت چکش خواری خوبی دارد و به سادگی اکسید نمی شود و در برابر خوردگی مقاوم است. قلع در بسیاری از آلیاژها مورد استفاده قرار می گیرد.
این عنصر چهل و نهمین عنصر فراوان پوسته زمین شناخته می شود. این بدان معنی است که حدود 0/001 % سهم پوسته زمین مخصوص به این فلز است. استحصال این فلز از سنگ معدن کاسیتریت (cassiterite) انجام می شود که حاوی ترکیبات اسیدی قَلع است.
قَلع از لحاظ مقاومت خوردگی، فلزی در رده متوسط محسوب می شود. این فلز در برابر حملات خوردگی توسط آب مقاومت می کند. اما در برابر بازهای قوی مورد حمله قرار می گیرد و تخریب می شود. این ماده را می توان جلا داد و بعنوان لایه ای محافظ برای محافظت سایر فلزات استفاده کرد. این فلز با تشکیل لایه پسیو (Passive Layer) از خوردگی فلز در محیط جلوگیری می کند.
در بین عناصر جدول تناوبی قَلع بیشترین تعداد ایزوتوپ پایدار را دارد
قلع در شرایط محیطی 10 ایزوتوپ پایدار دارد که در نوع خود جالب محسوب می شود. این عنصر بیشترین ایزوتوپ های پایدار را در بین عناصر جدول تناوبی دارد. این ایزوتوپ ها با عدد جرمی 112،114،115،116،117،118،119،120،122 و 124 در طبیعت یافت می شوند. ایزوتوپ های 116،118 و 120 فراوان ترین ایزوتوپ های این عنصر هستند که در میان آنها 120Sn جایگاه ویژه ای دارد. چرا که در بین روش های آنالیز مولکولی مثل آنالیز NMR به راحتی شناسایی می شود.
بعلاوه، تاکنون 31 ایزوتوپ ناپایدار از این عنصر شناسایی شده است که گستره ای از 99 تا 139 دارند. در بین این ایزوتوپ ها، 126Sn با 230000 سال بیشترین نیمه عمر را دارد. باقی ایزوتوپ های قَلع نیمه عمری کمتر از یک سال دارند.
فولاد رسول دلاکان
با سالها تجربۀ ارزشمند و گرانبها در عرصه تأمین و توزیع انواع ورق آلیاژی و انواع فولاد آلیاژی. با گواهینامه ها و آنالیزهای معتبری با ضمیمه نمودن آن محصولاتش به مشتریان خویش ارائه داده است. توانسته، رضایتمندی مشتریان خویش را همواره فراهم آورد.
صنعتگر شریف و گرامی از اینکه ما را جهت خرید کالا (فولاد آلیاژی) مورد نیاز خویش. انتخاب می نمایید از شما سپاسگزاریم.
ارتباط با ما
02128423820 -09122136675 – 09922704358
واتس آپ: 09122136675
اینستاگرام: fooladdalakan
فکس : 02128423820
ایمیل : fooladrasuldalakan@gmail.com
:: برچسبها:
قلع ,
فلز قلع ,
Tin ,
آرزیز ,
فولاد ضد زنگ ,
فولاد آلیاژی ,
مقاطع فولادی ,
پروفیل فولادی ,
فولاد زنگ نزن ,
لوله فولادی ,
ورق فولادی ,
میلگرد فولادی ,
سمه فولادی ,
فولاد ضد خوردگی ,
فولاد ضد سایش ,
نبشی ,
ناودانی ,
,
:: بازدید از این مطلب : 966
|
امتیاز مطلب : 9
|
تعداد امتیازدهندگان : 2
|
مجموع امتیاز : 2
تاریخ انتشار : شنبه 17 مهر 1400 |
نظرات ()
|
|
نوشته شده توسط : رسول دلاکان
متن کامل افزایش سختی کرنشی را می توانید با کلیک بر روی عبارت ((سختی کرنشی)) مشاهده نمایید.

افزایش سختی کرنشی ( Strain hardening) به پدیده افزایش سختی و استحکام فلزات داکتیل (شکل پذیر). در هنگام تغییر شکل پلاستیک (دائم یا غیر الاستیک) بیان می شود.
سختی کرنشی
گاهی به این پدیده work hardening به معنای افزایش سختی با کار Cold Hardening. به معنای افزایش سختی سرد (سرد نسبت به دمای ذوب فلز) نیز بیان می شود.
کارسختی یک نوع استحکام دهی به فلزات با تغییر شکل ماندگار در آن است. این استحکام در نتیجۀ جابجایی درون ساختار کریستال های ماده به وجود می آید. بسیاری از مواد نشکن با نقطۀ ذوب بالا مانند انواع مختلفی از پلیمرها می توانند با این روش استحکام یابند.
آلیاژهایی که به عملیات حرارتی قابلیت جوابگویی نداشته باشند مانند فولادهای کم کربن، می توانند کار سختی شوند. بسیاری از مواد در دمای پایین قابلیت کار سختی رویشان وجود ندارد. مانند ایندویوم در حالی که بقیۀ مواد می توانند سخت کاری شوند مانند مس خالص و آلومینیوم.
کار سختی بسته به نوع شرایط می تواند مطلوب یا نامطلوب باشد. یک نمودار نوع نامطلوب کار سختی هنگام ماشین کاری رخ می دهد. وقتی که تیغۀ برش از روی عدم توجه در ابتدا سطح قطعه کار را کارسختی می کند. این عمل باعث آسیب دیدن تیغه در براده برداری های ثانویه می شود. عملیات شکل دهی سرد معمولاً به چهار ریزشاخۀ اصلی تقسیم می شود؛ فشردن، خمش، حدیده کاری و برش.
افزایش سختی با کار مشکلی در ماشین کاری است که تقریباً همیشه توسط تراشکار ایجاد می شود. این اتفاق نتیجه مستقیم عمل اشتباهای در تراشکاری است. از جمله ابزارهای برش کند و سرعت بیش از اندازه ماشینکاری.
فولاد رسول دلاکان
با سالها تجربۀ ارزشمند و گرانبها در عرصه تأمین و توزیع انواع ورق آلیاژی و انواع فولاد آلیاژی. با گواهینامه ها و آنالیزهای معتبری با ضمیمه نمودن آن محصولاتش به مشتریان خویش ارائه داده است. توانسته، رضایتمندی مشتریان خویش را همواره فراهم آورد.
صنعتگر شریف و گرامی از اینکه ما را جهت خرید کالا (فولاد آلیاژی) مورد نیاز خویش. انتخاب می نمایید از شما سپاسگزاریم.
ارتباط با ما
02128423820 -09122136675 – 09922704358
واتس آپ: 09122136675
اینستاگرام: fooladdalakan
فکس : 02128423820
ایمیل : fooladrasuldalakan@gmail.com
:: برچسبها:
سختی کرنشی ,
افزایش سختی کرنشی ,
work hardening ,
Strain hardening ,
مقاطع فولادی ,
پروفیل فولادی ,
فولاد آلیاژی ,
ورق فولادی ,
میلگرد فولادی ,
تسمه فولادی ,
لوله فولادی ,
نبشی ,
ناودانی ,
فولاد ساختمانی ,
فولاد سازه ای ,
,
:: بازدید از این مطلب : 953
|
امتیاز مطلب : 19
|
تعداد امتیازدهندگان : 5
|
مجموع امتیاز : 5
تاریخ انتشار : شنبه 17 مهر 1400 |
نظرات ()
|
|
نوشته شده توسط : رسول دلاکان
متن کامل تیرآهن را می توانید با کلیک بر روی عبارت ((تیرآهن)) مشاهده نمایید.
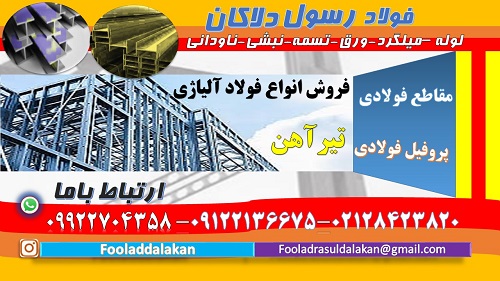
تیرآهن (Girder) اساسی ترین پروفیل ساختمانی است که بعضاً در پروژه های صنعتی نیز کاربرد دارد.
تیرآهن به سه صورت یافت می شود:
- IPE تیرآهن (استاندارد اروپا و ایران)
- تیرآهن INP (استاندارد چین و روسیه)
- IPB تیرآهن (بال پهن)
IPE تیرآهن و INP به ارتفاع 8 – 600 میلی متر و تیرآهن IPB به ارتفاع 100 – 1000 میلی متر تولید می شود. کاربرد تیر آهن در ساختمان به صورت ستون، خرپا، نعل درگاه، تیر در پوشش سقف ها و پل های لانه زنبوری استفاده می شود.
تیرآهن IPE
این تیرآهن معمولی و استاندارد I شکل در ایران وجود دارد. این تیرآهن طبق استاندارد اروپا تولید می شود و ضخامت بال آن ثابت است.
INP تیرآهن
تیرآهن I شکل که ضخامت بال آنها با ایجاد فاطه از جان تیرآهن می کاهد. که این استاندارد کارخانجات روسیه و چین می باشد.
IPB تیرآهن
H تیرآهن یا تیرآهن های عریض که در آنها طول بال ها نسبت به تیرآهن های IPE افزایش خواهد یافت.
نکته : علاومت V نشان دهنده سنگین بودن و علامت L نشان دهنده سبک بودن تیرآهن می باشد. به عنوان مثال IPBV نشان دهنده تیرآهن عریض سنگین و IPBL نشان دهنده تیرآهن عریض سبک می باشند.
فولاد رسول دلاکان
با سالها تجربۀ ارزشمند و گرانبها در عرصه تأمین و توزیع انواع ورق آلیاژی و انواع فولاد آلیاژی. با گواهینامه ها و آنالیزهای معتبری با ضمیمه نمودن آن محصولاتش به مشتریان خویش ارائه داده است. توانسته، رضایتمندی مشتریان خویش را همواره فراهم آورد.
صنعتگر شریف و گرامی از اینکه ما را جهت خرید کالا (فولاد آلیاژی) مورد نیاز خویش. انتخاب می نمایید از شما سپاسگزاریم.
ارتباط با ما
02128423820 -09122136675 – 09922704358
واتس آپ: 09122136675
اینستاگرام: fooladdalakan
ایمیل : fooladrasuldalakan@gmail.com
:: برچسبها:
تیرآهن ,
تیر ,
تیر فولادی ,
Girder ,
مقاطع فولادی ,
پروفیل فولادی ,
فولاد آلیاژی ,
لوله فولادی ,
ورق فولادی ,
تسمه فولادی ,
میلگرد فولادی ,
فولاد سازه ای ,
فولاد ساختمانی ,
,
:: بازدید از این مطلب : 856
|
امتیاز مطلب : 12
|
تعداد امتیازدهندگان : 5
|
مجموع امتیاز : 5
تاریخ انتشار : چهار شنبه 14 مهر 1400 |
نظرات ()
|
|
نوشته شده توسط : رسول دلاکان
متن کامل آبکاری را می توانید با کلیک بر روی عبارت ((پوشش دهی)) مشاهده نمایید.
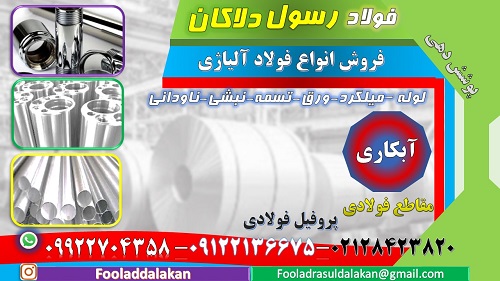
آبکاری یک روش پوشش دهی سطح است. که در آن یک فلز بر روی یک سطح رسانا پوشش د می شود. آبکاری برای صدها سال انجام می پذیرد. همچنین برای تکنولوژی مدرن اهمیت دارد.
پوشش دهی برای تزئینات اشیاء، مهار خوردگی، بهبود دوام پذیری، سخت شدن. بهبود پوشیدگی، کاهش اصطکاک، بهبود چشبندگی رنگ، تغییر هدایت، بهبود بازتابی IR، محافظت در برابر تابش و دیگر اهداف از جمله مزایای آبکاری می باشند.
لایه نشانی رسوبات نازک، اشیای کوچک را به عنوان یک اتم می پوشاند. بنابراین استفاده از پوشش در فناوری نانو به کار می رود.
چندین روش آبکاری وجود دارد. در یک روش یک سطح جامد با یک ورق فلزی پوشش دهی میشود. و سپس برای اتصال آنها از گرما و فشار استفاده می شود. دیگر تکنیک های پوشش دهی عبارتند از: آبکاری، رسوب بخار تحت خلاء و لایه نشانی پاششی. به تازگی پوشش دهی اغلب با استفاده از مایعات اشاره دارد. متالیزه کردن به فلز پوشش بر روی اشیای غیر فلزی اشاره دارد. ضخامت این لایه نازک فلزی، به ندرت از 0.025 میلی متر و یا 25 میکرون تجاوز می کند.
تاریخچه
به احتمال زیاد اولین آبکاری در دوران امپراتوری اشکانی انجام شد. ویلهام کونیگ دستیار موزه ملی عراق در دهه 1930 تعدادی از اشیاء نقره. بسیار ظریف از عراق باستان را که با لایه های بسیار نازک طلا را پوشش می دادند مشاهده کرد بود. و گمانه زنی کرد که آنها آبکاری اند. او ایده خود را با اشاره به باتری احتمالی اشکانی (پیل بغداد). که در سال 1938 در نزدیکی کلان شهر تیسفون، پایتخت اشکانیان (150 قبل از میلاد مسیح- 223 میلادی). و ساسانیان (224 تا 650 بعد از میلاد). امپراتوری های ایران کشف شد، تأکید کرد. این که آیا این دستگاه در واقع یک باتری بوده است یا خیر و از آن برای چه چیزی استفاده می شود. هنوز مورد بحث محققان است.
فولاد رسول دلاکان
با سالها تجربۀ ارزشمند و گرانبها در عرصه تأمین و توزیع انواع ورق آلیاژی و انواع فولاد آلیاژی. با گواهینامه ها و آنالیزهای معتبری با ضمیمه نمودن آن محصولاتش به مشتریان خویش ارائه داده است. توانسته، رضایتمندی مشتریان خویش را همواره فراهم آورد.
صنعتگر شریف و گرامی از اینکه ما را جهت خرید کالا (فولاد آلیاژی) مورد نیاز خویش. انتخاب می نمایید از شما سپاسگزاریم.
ارتباط با ما
02128423820 -09122136675 – 09922704358
واتس آپ: 09122136675
اینستاگرام: fooladdalakan
ایمیل : fooladrasuldalakan@gmail.com
:: برچسبها:
آبکاری ,
پوشش دهی سطح ,
فولاد آلیاژی ,
پوشش دهی الکترولس ,
پوشش دهی الکتریکی ,
مقاطع فولادی ,
پروفیل فولادی ,
لوله فولادی ,
ورق فولادی ,
تسمه فولادی ,
میلگرد فولادی ,
کروم ,
نیکل ,
,
:: بازدید از این مطلب : 930
|
امتیاز مطلب : 13
|
تعداد امتیازدهندگان : 4
|
مجموع امتیاز : 4
تاریخ انتشار : شنبه 10 مهر 1400 |
نظرات ()
|
|
نوشته شده توسط : رسول دلاکان
متن كامل فلز روي را مي توانيد با كليك بر روي عبارت (( فلز روي )) مشاهده نماييد.
روي ( Zinc ) عنصري است شيميايي با علامت اختصاري Zn كه داراي عدد اتمي 30 است. زينك فلزي است به رنگ سفيد متمايل به آبي كه براثر رطوبت هوا تيره رنگ مي شود .
و در حين احتراق رنگ سبز براقي توليد مي كند. زينك بعد از آهن ، آلومينيوم، و مس چهارمين فلز مورد استفاده در دنيا مي باشد. از موارد استفاده روي مي توان آلياژهاي مختلف از جمله برنج و پولاد گالوانيزه را نام برد.
تاريخچه
آلياژهايي كه زينك در آن ها قرار دارد. از قرون گذشته به كار مي رود. كالاهاي برنجي كه به 1000 تا 1400 سال پيش باز مي گردند. در فلسطين آثاري پيدا و همچنين اشياء داراي روي با 87% زينك را در ترانسيلوانيا ما قبل از تاريخ پيدا كرده اند. بعلت نقطه جوش پايين و واكنش شيميايي اين فلز (روي گسسته دود شده. و منجر به عدم دستيابي مي گشت.خصوصيات واقعي اين فلز در زمان باستان مشخص نشده بود.ساخت هم جوش برنج به روميان نسبت مي دهند. و مربوط به 30 سال پيش از ميلاد مي باشد.
آنها كالامين و مس را با يكديگر در بوته آهنگري حرارت مي دادند. كه در اين عمل اكسيد روي در كالامين كاهش مي يافت. و فلز زينك آزاد توسط مس به گير مي افتاد. و به شكل آلياژ مي شد. برنج توليدي يا در قالب قرار، يا با چكش به شكل هاي مختلف تبديل مي شد.
استخراج و تصفيه روي نا خالص در 1000 سال پيش از ميلاد مسيح در هند و چين انجام مي شد. در غرب نيز كشف فلز روي به Andreas Marggraf آلماني در سال 1746 بر مي گردد.
شرح توليد برنج در اروپاي غربي در كتاب هاي آلبرتوس مگنوس در سال 1284 به چشم مي خورد. اين فلز در قرن 16 به ميزان قابل توجه شناخته شد. Agricola در سال 1546 اعلام نمود. كه وقتي كه سنگ معدن روي گداخته شود. فلز سفيد قادر به انقباض است تا ديواره كوره را بتراشد. او در نوشته هاي خود به اين مسئله نيز اشاره كرد كه فلزي شبيه آن به نام Zircum در Silesia توليد مي شد.
پاراسليوس (متوفي به سال 1541) اولين كسي در غرب بود. كه گفت Zircum فلزي جديد است كه در مقايسه با فلزات ديگر خواص شيميايي جداگانه اي دارد. نتيجه آن است كه فلز روي زماني كشف گرديد كه Margaraf اكتشافاتي را شروع كرد. و در حقيقت فلز روي دو سال زودتر توسط شيميدان ديگري به نام Anton von swab تجزيه و توليد شد. اما تحقيقات Margraf جامع تر بود و بخاطر تحقيقات اين دو شخص آنها به عنوان كاشفين روي شناخته مي شوند. قبل از كشف تكنيك غوطه وري سولفيد روي Calamine تنها منبع معدني فلزي روي بوده است.
فولاد رسول دلاكان
با سالها تجربۀ ارزشمند و گرانبها در عرصه تأمين و توزيع انواع ورق آلياژي و انواع فولاد آلياژي. با گواهينامه ها و آناليزهاي معتبري با ضميمه نمودن آن محصولاتش به مشتريان خويش ارائه داده است. توانسته، رضايتمندي مشتريان خويش را همواره فراهم آورد.
صنعتگر شريف و گرامي از اينكه ما را جهت خريد كالا (فولاد آلياژي) مورد نياز خويش. انتخاب مي نماييد از شما سپاسگزاريم.
ارتباط با ما
02128423820 -09122136675 – 09922704358
واتس آپ: 09122136675
اينستاگرام: fooladdalakan
ايميل : fooladrasuldalakan@gmail.com
:: برچسبها:
ورق روی ,
فلز روی ,
زینک ,
Zinc ,
مقاطع فولادی ,
پروفیل فولادی ,
تولید فولاد ,
تولید ورق ,
فولاد آلیاژی ,
آلیاژ ,
میلگرد فولادی ,
ورق فولادی ,
لوله فولادی ,
,
:: بازدید از این مطلب : 951
|
امتیاز مطلب : 13
|
تعداد امتیازدهندگان : 5
|
مجموع امتیاز : 5
تاریخ انتشار : چهار شنبه 7 مهر 1400 |
نظرات ()
|
|
نوشته شده توسط : رسول دلاکان
متن كامل ريخته گري پيوسته را مي توانيد با كليك بر روي عبارت (( شكل دهي مداوم )) مشاهده نماييد.
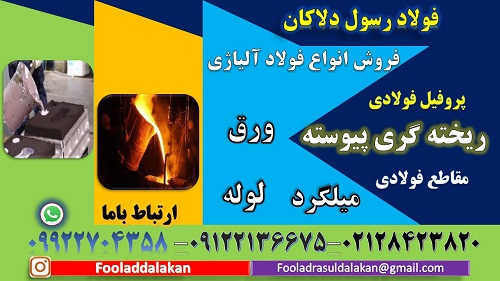
فرآيند ريختهگري پيوسته كه در آن براي كاربردهاي پسين فلز مذاب كه محصولات نيمه ساخته ريختهگَري مانند شمشال، شمشه، و تختال توليد مي شَود.
از زمان 1950، براي ساخت شمش فولادي در قالب هاي ثابت قرار مي گرفت.اين روش در آن زمان، جهت بالا رفتن كيفيت و كاهش صرف هزينه هاي توليد پيشرفت و گسترش بسياري پيدا كرد. اين روش به دليل داشتن هزينۀ ذاتي كم و كيفيت بيشتر و همچنين داشتن كنترل در طول فرآيند بسيار متداول است.
در واقع؛ شمش هاي آلومينيوم، برنج، مس، چدن و فولاد با مقطع مربعي، شش گوش و ساير مقطع توليد مي شوند. مذاب با نيروي ثقل به داخل كريستاليزاتور هدايت خواهد شد. شمش منجمد از مذاب، توسط سيستم كشنده به سمت پايين قرار مي گيرد.
هنري بسمر مشهور، حهت فرآيند بسمر به سال 1857 حق امتيازي،ريخته گري بين دو ميلۀ نورد دريافت داشت. در اين زمانه از اين روش، در بخش توليد ساخت نوار فولادي مورد استفاده قرار مي گيرد.
محدوده تقسيمات ريخته گري پيوسته
- ماشين هاي ريخته گري براي شمشال، شمشه و تختال طراحي مي گردند.
- نورد تختال براي شكل دهي قسمت هايي به كار مي روند كه پهناي بيشتري نسبت به كلفتي دارند.
- بطور قراردادي عرض اين تختال ها در محدودۀ 100 – 1600 ميلي متر. و ارتفاع 180 – 250 ميلي متر و طولي تا حداكثر 12 متر مي باشند. همينطور سرعت توليد و شكل دهي مواد به طور قراردادي حداكثر تا 1.4 متر بر دقيقه مي باشد.
- تختال هاي عريضتر حداكثر با 150 × 3250 ميلي متر نير موجود مي باشد.
- تختال هاي كلفت تر حداكثر با 450 × 2200 ميليمتر نيز موجود مي باشند. كه براي موارد خاصي از فولادها، به طور معمول از 200 ميلي متر تا 300 ميليمتر، كاربرد دارند.
- تختال نازك (فولاد كم كربن): 50 × 1680 ميلي متر. براي نوع بخصوصي از 40 ميلي متر تا 110 ميلي متر كلفتي را شامل مي شود. چ بسا به نوع طراحي هر دستگاه متفاوت است.
- بطور قراردادي نورد شمشه ها قسمت هاي بالا، 200 × 200 ميلي متر را توليد مواد مذاب مي كنند. طول شمشه مي تواند بين 4 – 10 متر متغير باشد.
- از حيث شكل دهي مواد بخش هاي خرد، نورد شمشال ها مورد استفاده. براي نمونه كمتر از 200 ميلي متر مربع و طول حداكثر 12 متر، سرعت توليد مواد مذاب مي تواند. تا 4 متر بر دقيقه پيش برود.
- قطر: 500 ميلي متر يا 140 ميلي متر
- باريكه (نوار نازك): كلفتي 2 – 5 ميلي متر و عرض 760 – 1330 ميلي متر دارد.
فولاد رسول دلاكان
با سالها تجربۀ ارزشمند و گرانبها در عرصه تأمين و توزيع انواع ورق آلياژي و انواع فولاد آلياژي. با گواهينامه ها و آناليزهاي معتبري با ضميمه نمودن آن محصولاتش به مشتريان خويش ارائه داده است. توانسته، رضايتمندي مشتريان خويش را همواره فراهم آورد.
صنعتگر شريف و گرامي از اينكه ما را جهت خريد كالا (فولاد آلياژي) مورد نياز خويش. انتخاب مي نماييد از شما سپاسگزاريم.
ارتباط با ما
02128423820 -09122136675 – 09922704358
واتس آپ: 09122136675
اينستاگرام: fooladdalakan
ايميل : fooladrasuldalakan@gmail.com
:: برچسبها:
ريخته گري ,
ريخته گري فولاد ,
ريخته گري آهن ,
ريخته گري پيوسته ,
ريخته گري مداوم ,
شكل دهي فولاد ,
شكل دهي آهن ,
آهنگري ,
مقاطع فولادي ,
پروفيل فولادي ,
فولاد آلياژي ,
dummy bar ,
,
:: بازدید از این مطلب : 875
|
امتیاز مطلب : 54
|
تعداد امتیازدهندگان : 16
|
مجموع امتیاز : 16
تاریخ انتشار : چهار شنبه 7 مهر 1400 |
نظرات ()
|
|
نوشته شده توسط : رسول دلاکان
ورق دورستات-فروش ورق ضد سایش-فولاد ضدسایش-فولاد آلیاژی ((قیمت مناسب))
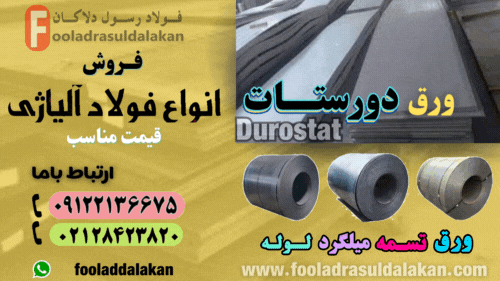
ورق دورستات (Durostat) یکی از محصولات تجاری شرکت اتریشی وستالپاین (Voestalpine) است. این نوع ورق های فولادی یکی از چندین نوع فولاد ضد سایش به شمار می روند. کمپانی وستالپاین با دانش خود قادر به تولید یکی از محصولات با کیفیت و خوب و معروف فولادی ضدسایش دنیا. را با درجه کیفی بسیار بالا و کاربردهای مختلف ایجاد و تبدیل به محصول نماید.
با توجه به اینکه این ورق ها در داخل کشور برای پروژه های مختلف استفاده می شود. و در صنایع ساخت فولادسازی بطور کامل شناخته و مورد قبول واقع و معروف است. این نوع محصول مورد بررسی قرار می گیرد.
آشنایی با ورق دورستات ورق فولادی بسیار مقاوم در کلاس جهانی
این ورق از بالاترین درجه سختی یا تافنس (Toughness) در بین انواع فولاد ضد سایش برخوردار است. با توجه به درجه سختی برینل 400 تا 600. مقاومت عالی در برابر فشار مکانیکی و سطح سایشی دارد.
این نوع ورقه ها چقرمگی بسیار بالایی در دمای پایین دارند. و جوش پذیری (Weldability) بسیار خوبی از خود نشان می دهند. جوش پذیری عالی به معنای این است. که با وجود ضخامت پایین ورق ها، نیازی به پیش گرمایش جهت جوشکاری نیست.
سختی ورق های دورستات چه بسا به عقیده بیشماری از تحلیل گران از کمپانی هایی که در حال کار و معتبر در صنعت فولاد، به الماس شباهت دارد. به همین دلیل کاربرد بیشتر در مواردی است. که درجه سختی و فاکتورهای محیطی شدید و خاص وجود داشته باشند.
باتوجه به ویژگی های بیان گشته؛باید انتظار داشت که ماندگاری و دوام بالایی برای ورقه ضدسایش دورستات متصور گردد. به نحوی که در اثر مصرف طولانی در گذر زمان، دچار پوسیدگی و فرسودگی نخواهد شد.
از دیگر ویژگی های ورق فولادی دورستات می توان به ماشین کاری (Machinability) آنها نام برد. که سازگار با دستگاه های مختلف تولید و پرداخت کاری اند. فولادهای ضد سایش دورستات فقط در ورق های فولادی ضد سایش مورد ساخت، تحت فرآیند کوئچینگ معمولی (Conventional Quenching یا CQ) اند که می توان آنرا مورد ارزیابی قرار داد.
پس از تولید نیز این ورقه ها نیازی به ترمیم کاری و رنگ آمیزی ندارند. در نتیجه خط تولید آنها سرعت بالا و دارای هزینه کمی است.
کاربرد ورق دورستات
طبق کاتالوگی که در سایت شرکت اتریشی دورستات مجود است. کاربردهای فراوانی برای این نوع ورق هاست. که نشان از کاربردپذیری بسیار بالا و کیفیت ساخت فوق العاده آنهاست.
موارد کاربرد: 1- ماشین های لایروبی 2- سطل لودر 3- ناودان ها 4- بدنه کمپرسی 5- ماشین های برف روبی 6- ماشین آلات بارگیری و نقل و انتقال. 7- سوپر استراکچرهای کامیون 8- محفظه های نگهداری آهن آلات و فلزات قراضه و اوراقی 9- صنایع معدن 10- صنایع تولید سیمان 11- ماشین آلات کشاورزی و...
فـــولاد رســـول دلاکــان
با سالها تجربه ارزشمند و گرانبها در عرصه تأمین و توزیع انواع ورق آلیاژی و انواع فولاد آلیاژی با گواهینامه ها و آنالیزهای معتبر با ضمیمه نمودن آن به محصولاتش آنرا به مشتریان خویش ارائه داده است. که توانسته رضایتمندی آنان را همواره فراهم آورد. صنعتگر شریف و گرامی از اینکه ما را جهت خرید کالا (فولاد آلیاژی) مورد نیاز خویش، انتخاب می نمایید از شما سپاسگزاریم.
ارتباط با ما 09122136675 02128423820 واتس آپ :09122136675 فکس: 02128423820 اینستاگرام :fooladdalakan ایمیل: fooladrasuldalakan@gmail.com
:: برچسبها:
ورق دورستات ,
Durostat ,
ورق ضد سایش ,
ورق ضد زنگ ,
فولاد آلیاژی ,
فولاد دورستات ,
فولاد ضد زنگ ,
فولاد زنگ نزن ,
ورق زنگ نزن ,
مقاطع فولادی ,
پروفیل فولادی ,
فولاد استحکام بالا ,
فولاد مقاوم بالا ,
,
:: بازدید از این مطلب : 1005
|
امتیاز مطلب : 19
|
تعداد امتیازدهندگان : 6
|
مجموع امتیاز : 6
تاریخ انتشار : شنبه 3 مهر 1400 |
نظرات ()
|
|
نوشته شده توسط : رسول دلاکان
متن کامل فولاد نیتراته را می توانید با کلیک بر روی عبارت (( فولاد نیتراته )) مشاهده نمایید.
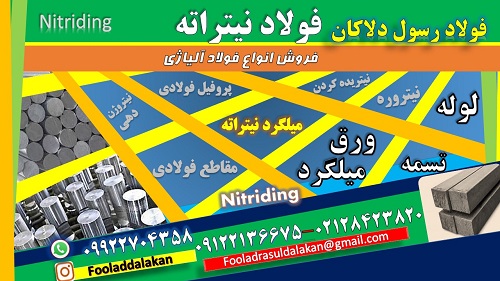
فولاد نیتراته یا فولاد نیتروره از فولادهای آلیاژی می باشد که توسط یک فرآیند شیمیایی تشکیل می شوند. در این فرآیند نیتروژن اتمی با عناصر سطح قطع تماس پیدا کرده. و نیتریدهای سخت و پایدار را تشکیل می دهد که به سطح فولاد نفوذ می کند. در اثر این فرآیند یک لایه سفید روی سطح فولاد پدید می آید که باعث افزایش سختی فولاد می شود.
هدف از نیتراته کردن فولادها
با نیتراته کردن، سطحی خیلی سخت و مقاوم به سایش به وجود می آید. به خاطر دمای بازپخت پایین (حدود 500 درجه سانتی گراد) تابیدگی خیلی جزئی در قطعه کار ایجاد می شود. و نیز به خاطر حذف عمل کوئنچ، هیچگونه تنشی در آن ایجاد نمی شود.
کاربرد فولاد نیتراته
فولادهای نیتراته در ابزار سازی برای ساخت انواع فرامین و نیز قالب های پرس کاری. مواد مصنوعی، لاستیک، قالب های تزریق، مواد ترموپلاستیکی. اجزا قالب های اکستروژن پیوسته مواد مصنوعی و ماشین های تزریق به کار می رود.
در نیتراته کردن فولادهای آلیاژی حاوی کروم، آلومینیوم و گاهی نیکل. دمای آنها را تا درجه حرارت 500 الی 520 درجه سانتیگراد در جریان گاز آمونیاک بازپخت می کنند. روش دیگری وجود دارد که در آن برای نیتراته کردن فولادهای آلیاژی فوق. آنها را در حمام مذاب نمک سیانید با درجه حرارت 550 الی 570 درجه سانتیگراد بازپخت می کنند.
در این عملیات حرارتی بازپخت، نیتروژن داخل سطح قطعه کار نفوذ کرده. و به خاطر پیوند با عناصر آلیاژی، باعث افزایش فوق العاده سختی در سطح آن می شود. با این روش به سختی ویکرز HV 1000 که معادل بیش از سختی راکول HRC 68 است. می توان دست یافت که این سختی را می توان تا دمای 500 درجه سانتی گراد بدون تغییر مشاهده کرد. اگر قرار است قسمت هایی از قطعه نرم باقی بماند. این قسمت ها با قلع اندود کاری پوشانده می شود.
فولاد نیتراته
ضخامت لایه نیتراته بسته به مدت زمان بازپخت، روش نیتراته و نوع فولاد نیتراته چند دهم میلیمتر می باشد. عیب این روش بازپخت طولانی مدت آن است. مدت زمان لازم برای عمق سخت کاری حدود 0/1mm. در نیتراته حمام نمک و گاز به ترتیب 2 و 8 ساعت می باشد.
از آنجا که تغییرات (گرادیان) سختی از سطح قطعه کار به طرف مغز آن آرام است. کنده شدن سطح سخت آن به سختی امکان پذیر است. با اینهمه از ایجاد لبه های تیز و پره های نازک در قطعه کار پرهیز شود. چون در این موارد عمل نیتراته از دو طرف انجام می پذیرد. مغزی چقرمه و نرم باقی نمی ماند. در قطعات جدار نازک لبه قطعات گرد و مدت زمان نیتراته کوتاه شود. بهسازی فولادها مفید است. زیرا در حالت بهسازی خواص مکانیکی بهتری داشته. و جهت ایجاد لایه نیتراته بدون عیب و محکم ساختار بهسازی شده است.
فولاد رسول دلاکان
با سالها تجربۀ ارزشمند و گرانبها در عرصه تأمین و توزیع انواع ورق آلیاژی و انواع فولاد آلیاژی. با گواهینامه ها و آنالیزهای معتبری با ضمیمه نمودن آن محصولاتش به مشتریان خویش ارائه داده است. توانسته، رضایتمندی مشتریان خویش را همواره فراهم آورد.
صنعتگر شریف و گرامی از اینکه ما را جهت خرید کالا (فولاد آلیاژی) مورد نیاز خویش. انتخاب می نمایید از شما سپاسگزاریم.
ارتباط با ما
02128423820 -09122136675 – 09922704358
واتس آپ: 09122136675
اینستاگرام: fooladdalakan
ایمیل : fooladrasuldalakan@gmail.com
:: برچسبها:
Nitriding ,
فولاد نیتراته ,
فولاد نیتروره ,
فولاد ابزار ,
فولاد آلیاژی ,
مقاطع فولادی ,
پروفیل فولادی ,
لوله فولادی ,
میلگرد فولادی ,
تسمه فولادی ,
ورق فولادی ,
میلگرد نیتراته ,
فولاد قالب سازی ,
فولاد ماشین کاری ,
,
:: بازدید از این مطلب : 959
|
امتیاز مطلب : 47
|
تعداد امتیازدهندگان : 14
|
مجموع امتیاز : 14
تاریخ انتشار : چهار شنبه 31 شهريور 1400 |
نظرات ()
|
|
|
|
|